- Главная
- Оборудование для печатных плат
- Оборудование для поверхностного монтажа
- Технологии производства плат и поверхностного монтажа
- Инструмент для печатных плат и Запасные части
- Материалы и Химикаты для печатных плат и поверхностного монтажа
- Гальваническое оборудование
- Лабораторное и аналитическое оборудование
- Сервис и техническое обслуживание
- Как нас найти
- Начало раздела
- Главный технолог
- Технологии производства
- Консультации
- Контакты
Обеспечение технологичности (DFM-design for manufacturing), с использованием инновационных технологий
Итак коротко о некоторых аспектах и существующих проблемах, которые позволят разработчикам и производителям печатных плат и электронных модулей более эффективно использовать DFM-технологии:
1. Для решения задач DFM необходимо знание всех инфраструктурных составляющих и понимание их взаимовлияния и взаимодействия. Ведь разработка любого проекта сводится к решению 3-х главных задач: функциональность, минимизация стоимости изготовления, надежность в эксплуатации.
2. DFM имеет смысл, как комплексная системадля всех инфраструктурных составляющих. Выпадение, полное или частичное, какой-либо из инфраструктурных составляющих, приводит к существенной деструкции всей системы и невыполнению, какой-либо из упомянутых выше задач, (чаще всего последних двух).
3. Одним из главных заблуждений разработчиков, с которыми я сталкивался в своей практике, является убеждение, что проблемы DFM (технологичности) являются значимыми, только на стадии серийного производства. В реальной жизни это приводит к необходимости кардинальной переработки проектов после их принятия на стадии прототипирования и при подготовке серийного или даже мелкосерийного производства, с соответствующим увеличением сроков Кстати большинство проектов спецтехники рассчитаны на серии несколько десятков штук, которые и серией-то в полном смысле нельзя назвать. На самом деле проблемы DFM должны в полной мере учитываться и решаться уже на стадии опытных образцов, а еще лучше прототипов и макетов.
4. Нормативно-техническая база еще одна из составляющих инфраструктуры, сдерживающая внедрение DFM из-за своей недоразвитости . Создавать собственную систему значит терять много времени. Хорошим подспорьем в решении этой задачи могут быть международные стандарты используемые хотя бы как справочные.
5. Существенной частью инфраструктуры DFM является освоение передовых перспективных технологических операций, позволяющих разработчикам реализовать новые функциональные характеристики электронных модулей, как правило в части увеличения плотности, скорости передачи сигнала,и т.п. Имею в виду такие актуальные на сегодняшний день операции как:
- прямое формирование рисунка, лазером или с помощью струйных принтеров;
- изготовление печатных плат методом послойного наращивания (SBU – Subsequent Вuilding – Up);
- планаризация путем заполнения отверстий гальваническими методами и органическими составами;
- встраивание пассивных и активных компонентов внутрь многослойных печатных плат ( в том числе в рамках « систем –в-корпусе» и микросборок).
На самом деле, как правило, задача проектирования для производства (DFM) сводится к тому, куда перераспределить трудоемкость:
- на стадию проектирования,
- или на стадию производства (подготовку производства, согласование правок проекта, трудоемкость изготовления с учетом нескольких итерраций, трудоемкость исправления технологических дефектов, трудоемкость гарантийного обслуживания).
Теперь ряд конкретных рекомендаций по соблюдению правил DFM.
Надо сказать, что хотя большинство действий по соблюдению правил DFM проводятся на рисунке наружных слоев печатных плат, направлены они на обеспечение через указанные характеристики симметрии действия сил поверхностного натяжения и бездефектного формирования паяных соединений. Это необходимо для того, чтобы не происходило сдвига компонента в процессе расплавления припоя. Нетехнологичные конструкторские решения, не обеспечивающие выполнения этого условия, необходимо отсеивать на стадии подготовки производства (если они не выполнены на стадии разработки).
Итак основой формирования паяного соединения является фаза смачивания расплавленным припоем вывода и ламели – поэтому дефекты паяных соединений поверхностного монтажа, как правило, связаны с разницей силы поверхностного натяжения расплавленного припоя на разных выводах компонентов , которая в значительной степени зависит от следующих характеристик:
- от периметра ламели;
- количества припоя на ламели;
- вязкости припоя.
Обязанностью конструктора в рамках обеспечения задач DFM является обеспечение этих требований. Несоблюдение при конструировании требований симметрии сил поверхностного натяжения приводит к образованию дефектов паяных соединений (в первую очередь «могильных камней).
На рис.1 показана часто встречающаяся конструкторская ошибка при формировании ламелей на полигоне. Как было сказано выше от периметра ламели зависит сила поверхностного натяжения. Разница периметров противоположных ламелей на рис. 1 = 8∆ (где ∆ зазор между проводящим рисунком и освобождением в ПМ). На миниатюрных компонентах относительная разница между периметрами 2(А+В) и 2(А+В) +8∆} может быть значительной, а, учитывая малый вес миниатюрных компонентов, это приводит к осевому смещению - вплоть до образования «могильного камня».
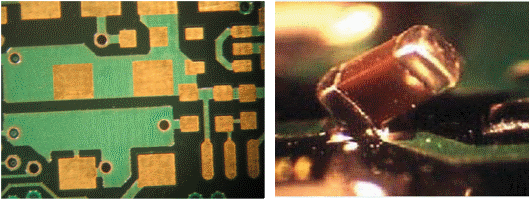
провоцирующее образование «могильного камня»
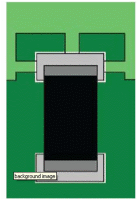
выполненный в соответствии с правилами DFM.
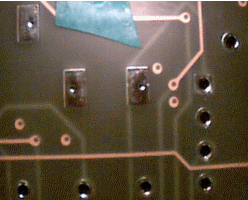
Необходимо при конструировании ламелей на полигоне делать разделение по периметру ламели и соединять ее с полигоном узкими перемычками. В этом случае не возникает большой разницы длины периметров ламелей и соответственно разницы сил поверхностного натяжения. (Рис.2.).
Еще одна типовая конструкторская ошибка - расположение отверстия в ламелях под пайку, что приводит к эффекту - который называется «воровство припоя отверстием» (такой устойчивый термин в технической литературе). Неконтролируемое количество припоя на ламели, связанное с этим эффектом, провоцирует возникновение дефекта, также связанного с разницей сил поверхностного натяжения на противоположных ламелях компонентов.
Один из примеров борьбы с «воровством припоя отверстием». Отделение ламели от отверстия перемычкой ПМ. При этом перемычка должна быть достаточно широкой (≥ 0,5мм).

отделение отверстия перемычкой ПМ.
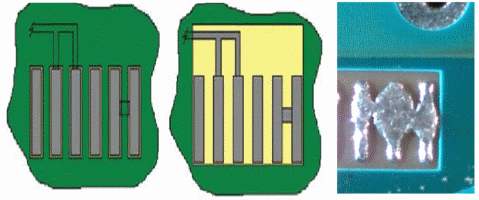
А вот еще один пример распространенного нарушения правил DFM, приводящего к снижению технологичности и ухудшению качества паяных соединений. При конструировании электрическое соединение соседних ламелей должно выполняться на периферии посадочного места и закрываться паяльной маской. Наличие электрических соединений внутри посадочного места затрудняет для оператора визуального контроля возможность отличить короткое замыкание, связанное с образованием мостиков припоя от схемного электрического соединения. В том числе следует иметь ввиду, что паяльная маска с таких соединений часто отлетает.
Несколько слов о проектировании посадочных мест компонентов BGA.
Пайка компонентов BGA один из наиболее сложных процессов в монтаже. Тем более, что количество выводов у этих компонентов растет при том, что сами компоненты становятся миниатюрнее.
Все паяные соединения надо контролировать. Большинство из них можно контролировать визуально. Но есть соединения, корректный контроль которых ( в частности паяных соединений BGA) возможен только рентгеном . Однако анализ рентгенограмм «требует комментариев». Необходим большой опыт оператора и понимание им физики процесса рентгеновского контроля для толкования обычных 2D рентгенограмм. Инструмент, облегчающий анализ рентгенограмм, – доработка конструктором посадочного места BGA, что также относится к области задач DFM (Рис.6.)
Как не один раз было сказано определяющим моментом формирования качественного паяного соединения является наличие смачивания. Доработка конструктором посадочного места существенно облегчает процедуру определения наличия смачивания. Доработка заключается в придании КП на посадочном месте BGA определенной формы (с удлинением).
(Рекомендуемые размерные соотношения доработанных КП: D≈4L) При наличии смачивания форма шарика на рентгенограмме становится вытянутой, и 2D рентгенограмма доработанного посадочного места позволяет с легкостью определить наличие смачивания на каждой КП.
В последнее время принято конструировать печатных плат с большим количеством компонентов BGA. Количество их выводов растет, шаги уменьшаются. Рассказанное становится на мой взгляд все более актуальным.

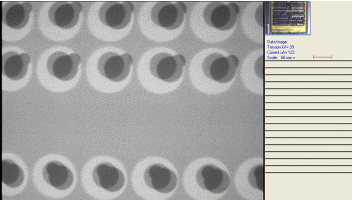
смонтированного на доработанном посадочном месте
Здесь были рассмотрены некоторые аспекты задачи проектирования для производства, с точки зрения обеспечения норм технологичности при проектировании. Эти аспекты , конечно, относятся в первую очередь к проектированию и изготовлению прецизионнных печатных плат, но вполне актуальны и при производстве печатных плат 3-4 класса точности. Как уже говорилось ранее соблюдение норм DFM приводит к сокращению трудоемкости, увеличению % выхода годных, повышению эксплуатационной надежности выпускаемых изделий.
Буду рад, если кому-то изложенные выше сведения оказались интересными или полезными. Подробности, разъяснения, любые вопросы - по моим контактам.
Это, что касается конструкторского обеспечения DFM. Но есть и технологический аспект, о нем кратко уже говорилось выше. Он касается в первую очередь расширения технических возможностей производства за счет освоения инновационного технологического оборудования и освоения инновационных технологических операций, что конечно должно быть в первую очередь интересно для технологов, для более четкого формулирования требований к правилам проектирования, обеспечивающих технологичность.
Очень часто в практической деятельности приходится сталкиваться с ситуацией, когда разработчик закладывает в конструкторскую документацию (КД ) необоснованно жесткие требования (типа - на всякий случай, хуже не будет) с целью «повышения надежности». А на самом деле, в случае, если требования КД не соответствуют возможностям производства, возникает противоположный эффект. Статистически доказано, что чем выше % выхода годных на приемо-сдаточных испытаниях и чем меньше количество, исправляемых дефектов, в процессе производства, тем выше надежность изделия, и наоборот.
По-видимому, это связано с тем, что часть дефектов пропускается при контроле, а часть скрытых дефектов ещё не проявляется при выходном контроле, но начинают проявляться на этапе эксплуатации. В этой связи очень важно для каждого конкретного производства во-первых иметь правила проектирования и во-вторых при запуске проекта корректировать КД с точки зрения максимально возможного расширения допусков на точность, поддержания технологических режимов на каждой из операций технологического процесса, естественно при сохранении требуемых технических характеристик изделия. Здесь очень важны уровень и глубина сотрудничества разработчика и технологов производства.
Казалось бы целесообразнее уделить больше внимания проектированию. Ведь проектирование делается один раз, а изготовление, как правило, - несколько. Однако , увы, до сих пор нет четкого осознания этого ни у разработчиков, ни у организаторов производства. Поэтому одной из ключевых задач раздела представляется формирование более тесного и глубокого взаимопонимания между конструкторами и технологами.
Таким образом задачи DFM являются существенными для снижения стоимости изготовления печатных плат и электронных модулей, обеспечения минимальной трудоемкости и максимального процента выхода годных при производстве. Если эти условия не соблюдаются разработчиком проекта, они должны быть доработаны на производстве (с учетом его конкретных возможностей) подразделением подготовки производства.