- Главная
- Оборудование для печатных плат
- Оборудование для поверхностного монтажа
- Технологии производства плат и поверхностного монтажа
- Инструмент для печатных плат и Запасные части
- Материалы и Химикаты для печатных плат и поверхностного монтажа
- Гальваническое оборудование
- Лабораторное и аналитическое оборудование
- Сервис и техническое обслуживание
- Как нас найти
- Начало раздела
- Оборудование
- Поддержка
- Справка
- Контакты
Особенности производства высокочастотных печатных плат
Объем информации, передаваемой по беспроводным сетям, резко увеличился с значительным ростом доступа в Интернет ( развитие техники IoT), увеличением числа мобильных телефонов и других портативных устройств, также различных военных и аэрокосмических применений, эксплуатирующих высокочастотные печатные платы (ВЧ ПП) в жестких условиях эксплуатации. Передача высокоскоростного радиосигнала все чаще требуется в печатных платах для обработки большого объема данных. Скорость передачи сигналов внутри систем тоже увеличивается. Это повлияло на возникновение высокого интереса среди специалистов к организации производства высокочастотных печатных плат.
В последнее время в практике общения с коллегами-специалистами приходится часто обсуждать и сравнивать различные методы выполнения операций в техпроцессе изготовления печатных плат. При этом самый распространенный вопрос: « Назовите наилучший метод выполнения операций». Ответ на этот вопрос для себя я нашел давно: « Не существует панацей в технике печатных плат, так же как, впрочем, их не существует и во всей остальной жизни. Каждый из альтернативных методов имеет свои преимущества и, поэтому, имеет право на существование, но при этом имеет и свои недостатки. (За все в этой жизни приходится платить)». Кроме того следует отметить, что в нашей отрасли скорость научно-технического прогресса очень велика и какой-либо догматизм при анализе новых технологий, а также ссылки на мнения авторитетов не допустимы.
Исходя из этого, при выборе какого-либо технологического метода, необходимо:
- во-первых, четко представлять себе все его преимущества и все недостатки;
- во-вторых, учитывая конкретные условия производства и номенклатуру выпускаемых печатных плат и электронных модулей ( ЭМ) ( по объемам, конструктивной сложности и т.п.), выбрать такой метод, который позволил бы в полной мере реализовать его преимущества и одновременно минимизировать влияние имеющихся у него недостатков.
Это очень непростая, но очень увлекательная задача и при ее решении в полной мере может проявиться творческий и профессиональный потенциал технологов, при этом не стоит ждать чудес – работают только фундаментальные законы, в основном физики и химии, немножко математики и биологии. При этом использование фирменных концентратов - это уже прочно сложившаяся мировая практика, особенно в высокотехнологичных производствах. Технологу необходимо лишь строго соблюдать технологический регламент, прописанный поставщиком. Вся ответственность за результат ложится на поставщика концентратов. Производственникам необходимо лишь разобраться, какая химия и оборудование лучше, не входя в подробности составов химии и конструктивных особенностей.
Все организации, так или иначе, имеют отношение к «проектированию для производства» (DFM - design for manufacturing). Путем нескольких итераций происходит «приработка» заказчика к стороннему (контрактному) исполнителю.
Основные источники проблем, возникающие на этом пути следующие:
1. При ведении разработки точно не определен производитель.
2. Если производитель определен, разработчик не учитывает возможности производства (причины разные, одна из распространенных – элементарно лень знакомиться с технологическими параметрами производства и непонимание, зачем вообще это необходимо - «диктат разработчика»).
3. Изготовитель не сформировал конструкторско-технологические нормы (КТН) своей производственной базы, или сформировал их не полно и/или не четко.
Итак коротко о некоторых аспектах и существующих проблемах, которые позволят разработчикам и производителям ПП и ЭМ более эффективно использовать DFM-технологии:
1. Для решения задач DFM необходимо знание всех инфраструктурных составляющих и понимание их взаимовлияния и взаимодействия. Ведь разработка любого проекта сводится к решению следующих главных задач: обеспечение функциональности, минимизация стоимости изготовления, надежность в эксплуатации.
2. DFM имеет смысл, как комплексная система для всех инфраструктурных составляющих. Выпадение, полное или частичное, какой-либо из инфраструктурных составляющих, приводит к существенной деструкции всей системы и невыполнению, какой-либо из упомянутых выше главных задач, (чаще всего последних двух).
3. Одним из главных заблуждений разработчиков, с которыми я сталкивался в своей практике, является убеждение, что проблемы DFM (технологичности) являются значимыми, только на стадии серийного производства. В реальной жизни это приводит к необходимости кардинальной переработки проектов после их принятия на стадии прототипирования и при подготовке серийного или даже мелкосерийного производства, с соответствующим увеличением сроков. Кстати большинство проектов спецтехники рассчитаны на серии несколько десятков штук, которые и серией-то в полном смысле нельзя назвать. На самом деле проблемы DFM должны в полной мере учитываться и решаться уже на стадии опытных образцов, а еще лучше прототипов и макетов.
5. Нормативно-техническая база еще одна из составляющих инфраструктуры, сдерживающая внедрение DFM из-за своей недоразвитости.
6. Существенной частью инфраструктуры DFM является освоение передовых перспективных технологических операций, позволяющих разработчикам реализовать новые функциональные характеристики электронных модулей, как правило в части увеличения конструктивной плотности, скорости передачи сигнала, и т.п. Имею в виду такие актуальные на сегодняшний день операции как:
- - прямое формирование рисунка, лазером или с помощью струйных принтеров;
- - изготовление ПП методом послойного наращивания (SBU – Subsequent Вuilding – Up);
- - планаризация путем заполнения отверстий гальваническими методами и органическими составами;
- - встраивание пассивных и активных компонентов внутрь МПП ( в том числе в рамках « систем –в-корпусе» и микросборок).
В отечественной, а чаще в зарубежной технической литературе встречаются следующие рассуждения:
«На сегодняшний день проектирование с учетом технологических требований часто не проводится, чтобы проекты были переданы в производство в более короткие сроки. Однако это выливается в создание труднореализуемых изделий. Если бы была упорядочена и внедрена технология ввода в производство нового изделия с учетом требований DFM, это позволило бы проводить готовые проекты с учетом технологических возможностей конкретного производства в соответствии с полными проектными требованиями, а также это значительно повысило бы качество изделий. Результатом стало бы создание большего числа оптимизированных проектов, которые будут попадать на рынок быстрее и с меньшим количеством редакционных итераций.»
На самом деле, как правило, задача «проектирования для производства» сводится к тому, куда перераспределить трудоемкость:
- - на стадию проектирования,
- - или на стадию производства (подготовку производства, согласование правок проекта, трудоемкость изготовления с учетом нескольких итераций, трудоемкость исправления технологических дефектов, трудоемкость гарантийного обслуживания).
Решение этого вопроса лежит целиком в компетенции организаторов и руководителей разработки и изготовления современной РЭА.
Развитие отрасли происходит с очень высокой скоростью и возможно приведенные выше рассуждения частично устарели. Но неизменной остается основная задача DFM
- - функциональность, минимизация стоимости изготовления, обеспечение надежности ПП в эксплуатации.
Основной задачей при изготовлении высокочастотных печатных плат является минимизация потерь, обеспечивающая эффективность передачи ВЧ сигнала.
Вносимые потери радиочастотного сигнала представляют собой ухудшение мощности сигнала в результате включения устройства в линию передачи. Выражаемые в децибелах (дБ), вносимые потери становятся значительными на печатной плате на более высоких частотах ГГц.
Фактор потерь.
Потери при передаче можно разделить на диэлектрические потери и потери в проводнике.
Полная потеря линии передачи называется вносимой потерей и является суммой нескольких других потерь.
Упрощенный вид этих потерь следующий:
αT = αC + αD + αR + αL
Общие потери (вносимые потери, αT) состоят из потерь в проводнике (αC), диэлектрике (αD), потерь излучения (αR) и потерь от утечки (αL).
- На потери в проводнике влияют размер или вид проводника, и они увеличиваются пропорционально кв. корню из частоты (f). Чем больше увеличивается частота, тем более сигнал концентрируется на поверхности меди. Следовательно, область прохождения тока ограничена (потеря за счет скин-эффекта). Кроме того, если поверхность проводника шероховатая, потери передачи на высокой частоте будут больше, чем для гладкой поверхности. Это связано с тем, что протеканию тока препятствует шероховатость поверхности проводника (потеря за счет эффекта шероховатости поверхности).
- На диэлектрические потери влияют диэлектрические свойства (диэлектрическая проницаемость (ε или Dk) коэффициент рассеяния (tg δ или Df)) изоляционных материалов, и они увеличиваются пропорционально частоте (f). Диэлектрические потери связаные с коэффициентом рассеяния (Df) подложки, используемой для изготовления печатной платы имеют малое значение, так как большинство высокочастотных схемных материалов имеют Df менее 0,005 и оказывают слабое влияние на диэлектрические потери.
- Кроме того материалы, используемые в технологии печатных плат, как правило, имеют очень высокое объемное сопротивление и благодаря этому свойству потери от утечки также минимальны.
- Толщина скин слоя является основной причиной потерь в проводнике, а это параметр проводника, по которому течет электрический ток. При постоянном токе (0 Гц) электрический ток будет использовать всю площадь поперечного сечения проводника. По мере увеличения частоты - ток будет использовать только наружный слой проводника и при высоких частотах глубина скин слоя часто намного меньше, чем 2 микрона. Так пример, глубина скин слоя в медном проводнике с частотой 1 ГГц составляет 2,08 микрона), при 10 ГГц - 0,66 микрона, а при 50 Ггц ≈ 0,28 микрона.
Математическое соотношение для глубины скин слоя составляет:
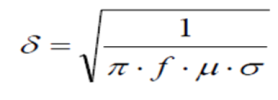
Где δ - глубина скин-слоя;
f – частота;
μ - магнитная проницаемость;
σ – проводимость.
Магнитная проницаемость является свойством материала при изменении магнитных полей и большинство диэлектриков, используемых в индустрии печатных плат, имеют проницаемость свободного пространства.
Проводимость металла может влиять на глубину скин-слоя, и чем ниже удельная электропроводность (более резистивная), тем больше глубина скин слоя.
До определенных частот хороший эффект дает использование безникелевых финишных покрытий (ЕРIG, ENEPIG, RAIG). С одной стороны они позволяют уменьшить потери за счет существенно более низкого удельного сопротивления меди, палладия, золота, чем никеля. А с другой хорошо защищают поверхность проводников, не требуя дополнительного диэлектрического покрытия с высокой Dk.
Другой проблемой, связанной с потерей в проводнике, является шероховатость поверхности проводника. Когда поверхность проводника шероховата, это вызовет более длинный путь распространения волны и создаст больше потерь. Когда глубина скин слоя примерно равна размеру шероховатой поверхности меди, шероховатость будет иметь значительное влияние на потери в проводнике.
УВЕЛИЧЕНИЕ ЧАСТОТЫ
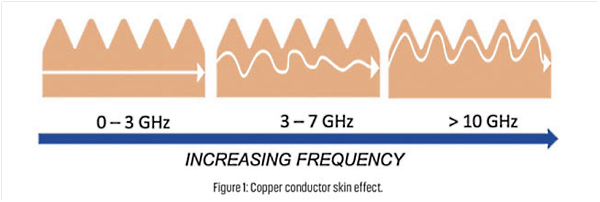
Рис.1. Зависимость пути протекания ВЧ сигнала от шероховатости и частоты (скин-эффект).
Последнее время производители медной фольги разработали новые типы медной фольги, чтобы решить проблемы потери сигнала из-за шероховатости - VLP (фольга с очень низким профилем шероховатости) и HVLP (фольга с сверх низким профилем шероховатости).
Кроме того, если раньше при подготовке медной поверхности перед прессованием делали рабочие растворы, которые увеличивали шероховатость для улучшения механической связи с диэлектриком и одновременно формировавшие адгезионный слой для увеличения химической связи ; то при изготовлении высокочастотных печатных плат для минимизации потерь пользуются рабочими растворами формирующими в первую очередь адгезионный слой. ( Например ф. Dow – Dupount рекомендует в рабочем растворе Bond Film Treatment вместо соотношения составов для развития шероховатости и формирования адгезионного слоя 100% к 100% использовать соотношение 60% к 100%)
Три наиболее распространенные линии микроволновой передачи, показаны на рисунке
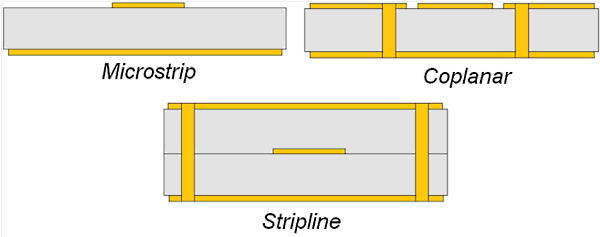
Рисунок 2. Вид поперечного разреза трех линий передачи.
Микрополосковая линия передачи, показанная в верхнем левом углу рисунка 1, представляет собой простую двухслойную схему с сигналом проводник сверху и плоскостью заземления снизу. Эта структура, вероятно, является наиболее распространенной структурой в печатных платах СВЧ однако, часто это только внешний слой многослойной печатной платы.
Микрополосковые схемы имеют три механизма потерь, которые обсуждались ранее, которые составляют общие вносимые потери. Каждая из этих потерь будет более или менее значительной в зависимости от толщины платы. Для тонкой платы потери в проводнике будут доминировать, но если это грубая медь, потери в проводнике будут очень значительными.
Если микрополосковая схема использует более толстую подложку, потери в проводнике будут менее значительными.
Другим фактором увеличения потерь в проводнике является степень трапецевидности поперечного сечения проводников высокочастотных печатных плат. Для лучшего понимания этого фактора следует ввести понятие фактора травления.
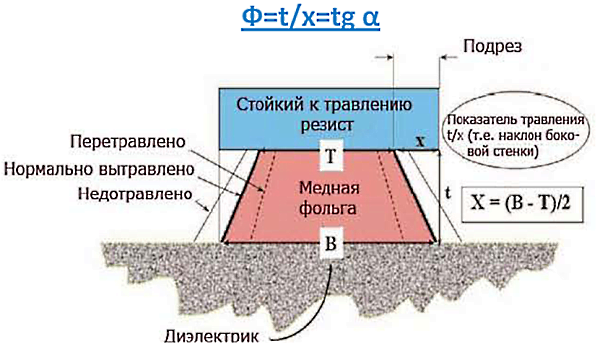
Рис. 3. Фактор травления (Ф).
При необходимости формирования прецизионных проводников и зазоров (75/75 мкм, а тем более 50/50 мкм при толщинах меди 30 и более мкм) становится актуальной проблематика технологического обеспечения малых допусков на ширины проводников и зазоров (т.е. обеспечение равномерности травления по всему рабочему полю) и возможность формирования проводников с высоким фактором травления ( 4-5 и более – т.е. формирования проводников с вертикальными боковыми стенками) (Рис. 4)
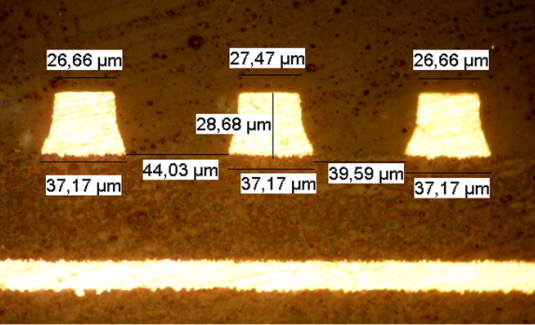
Рис. 4. Фольга 30 мкм , проводник /зазор - 40/40 мкм, реализованные на оборудовании ф. Schmid.
Особенности процесса щелочного травления не позволяют получить фактор травления больше 2,5-3, в то время как кислым травлением удается получить фактор травления в диапазоне 4-6. Способность формирования прецизионных (40/40 мкм) проводников/зазоров с высоким ( св. 5) фактором травления на инновационном оборудовании ф. Schmid или аналогичном открывает перед производственниками возможность применения технологии «тентинг». Это особенно актуально при производстве высокочастотных печатных плат. Дело в том, что практически все оборудование АОИ позволяет измерить только максимальную ширину поперечного сечения проводника. В этой связи формирование проводников в высоким фактором травления обеспечит минимизацию проводниковых потерь в высокочастотных печатных плат. Этот процесс обеспечивает установка прецизионного травления Infinity Line с технологией NEO.
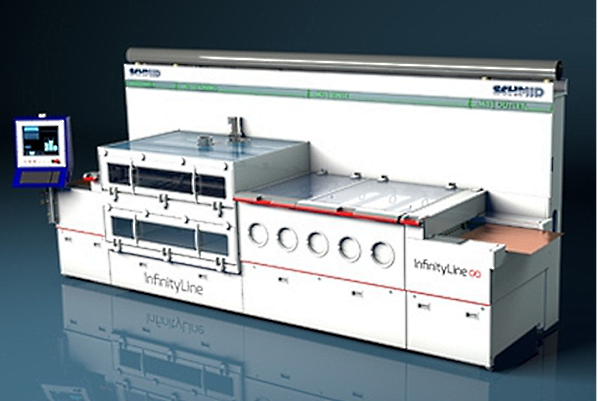
Рис.5. Установка прецизионного травления Infinity Line с технологией NEO.
В качестве примера инновационного оборудования, решающего эти задачи, можно привести травильные машины ф. Schmid, оснащенные новыми травильными опциями (NEO- new etching options) (Рис. 5 ):
- дополнительным модулем интермиттирующего травления;
- системой вакуумного травления (Рис. 6 а);
- оптимизированной конструкцией распылительных форсунок с расширенным до 4-х бар интервалом рабочего давления (Рис. 6 б);
- обновленной системой управления динамикой потока травильного раствора;
- усовершенствованной транспортной системой.
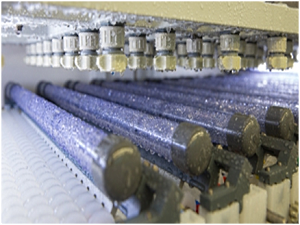
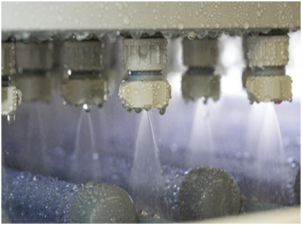
Рис. 6. Система вакуумного травления и оптимизированная конструкция распылительных форсунок установки травления ф. Schmid.
Эти опции позволяют на горизонтальной конвеерной машине стабильно получать результат 40/40 мкм с фактором травления 5 и более. Пристыковка к этим машинам систем регенерации решает задачу обеспечения экологических проблем и замкнутого водооборота. (Рис.7.). Кроме того система регенерации позволяет в течении долгого времени поддерживать стабильные параметры травильного раствора по содержанию меди (плотности) и pH.
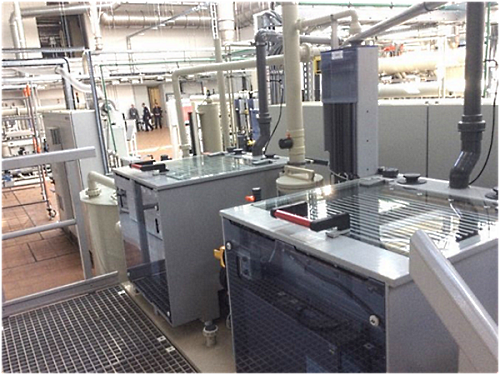
Рис. 7. Система регенерации травильного раствора ф. Sigma.
Регенерация также позволяет организовать замкнутый производственный цикл и, имея на выходе процесса хорошо ликвидную чистую медь, в значительной мере компенсировать производственные издержки.
Еще несколько слов для популяризации «тентинга» (кислого травления).
Ранее позитивный (полуаддитивный) метод считался способным формировать более прецизионный рисунок, чем негативный («тентинг») метод. Однако с появлением травильных машин, обеспечивающих высокий фактор травления (до 5-6 на толщинах меди 30 мкм и более) и высокую равномерность травления по полю заготовки (Infinity NEO ф. Шмид и аналогичных), а также широкого использования сквозных отверстий малого диаметра - позитивный метод, (особенно учитывая его многооперационность), утратил свои преимущества по сравнению с «тентингом».
Возможность получения высоких значений «фактора травления» делает кислое травление (а вместе с ним негативный метод, и «тентинг», как одну из его разновидностей) очень привлекательным для получения прецизионного ( в том числе в части формирования прямоугольного поперечного сечения) проводящего рисунка. Напомню, что при этом негативный метод («тентинг») обладает еще рядом неоспоримых преимуществ.
1. Короткий техпроцесс.
Это связано главным образом с отсутствием в технологической цепочке операций связанных с необходимостью наносить, а потом снимать металлорезист.
2. Высокое качество гальванического осадка.
При тентинге процесс гальванической металлизации происходит по всей поверхности заготовки, когда на ней нет фоторезиста. Отсутствие больших масс органического вещества в ваннах гальванической металлизации позволяет легко формировать высоко пластичный медный осадок в металлизированных отверстиях, что существенно повышает надежность печатной платы, особенно при групповой пайке принятой в технологии поверхностного монтажа.
3. Постоянная величина тока при гальванической металлизации - определяемая постоянной площадью металлизации из-за отсутствия рисунка.
Это очень удобно в условиях многономенклатурного производства и уменьшает вероятность возникновения субъективных ошибок оператора - при установке режимов линии гальванической металлизации, а также технологов - при подготовке производства и расчете площади металлизации и выравнивающих рамок.
4. Единая методика формирования внутренних и наружных слоев. Внутренние слои всегда изготавливаются негативным (субтрактивным) методом. Использование единой техники изготовления наружных и внутренних слоев – существенно упрощает организацию производства.
5. Одна программа сверления.
Тот факт, что металлизация отверстий при тентинге происходит по сплошной заготовке, позволяет до металлизации просверлить, как металлизированные, так и не металлизированные (как правило - крепежные) отверстия. В последствии при фотолитографическом формировании рисунка отверстия, которые не должны иметь металлизацию не тентируются (в фотошаблоне наружного слоя) и металлизация из них удаляется при операции травления. Это сокращает техпроцесс и увеличивает точность совмещения массивов не металлизированных и металлизированных отверстий с рисунком наружного слоя.
6. По сравнению с позитивным процессом, в котором в качестве металлорезиста используется сплав олово-свинец , существенным преимуществом тентинга является отсутствие свинца в стоках. В последнее время, правда, этот металлорезист повсеместно вытесняется чистым оловом.
7. Отсутствие ванны металлорезиста (снижение издержек на приобретение компонентов рабочих растворов, оловянных или олово-свинцовых анодов и т.п.) и оборудования для снятия металлорезиста.
Главным недостатком тентинга (а именно этот вариант негативного метода конкурирует с комбинированным позитивным процессом) является, как многие считают, худшая по сравнению с позитивным методом прецизионность. Выше я попытался доказать, что возможность получения больших значений фактора травления в сочетании с использованием передового технологического оборудования делает «тентинг» очень привлекательным (с учетом всех его положительных свойств) для изготовления ВЧ печатных плат с прецизионным рисунком.
Обратное сверление (back drilling) и эффект излучения
Ещё одним фактором влияющим на минимизацию потерь в высокочастотных печатных платах формируемым технологическим методом является ликвидация мест возможного отражения сигнала, которое в первую очередь производится использованием сверлильного станка с опцией обратного сверления (backdrilling).
Чтобы уменьшить излучения в линии передачи, производители печатных плат разрабатывают технику обратного сверления . При излучении сигнал проходит более длинный обратный путь, чем должен. Операция заключается в удалении металлизации сквозных отверстий на участках не лежащих на пути прямой передачи ВЧ сигнала. Обратное сверление может устранить индуктивность на дополнительном пути и улучшить характеристики потерь. ООО «РТС Инжиниринг» рекомендует использовать для решения этой задачи сверлильные станки ф.Плюритек.
Выводы.
Общефилосовский подход к разработке высокочастотных печатных плат заключается в обеспечении функциональности, минимизации стоимости изготовления, обеспечении надежности высокочастотных печатных плат в эксплуатации. Решение этого вопроса лежит целиком в компетенции организаторов и руководителей разработки и изготовления современной РЭА в том числе высокочастотной и во многом зависит от глубины и эффективности взаимодействия разработчиков и технологов.
Основной задачей при изготовлении высокочастотных печатных плат является минимизация потерь, обеспечивающая эффективность передачи ВЧ сигнала.
Технолгически эта задача решается следующими способами:
а) использование безникелевых финишных покрытий (ЕРIG, ENEPIG, RAIG);
б) минимизация шероховатости за счет использования ламинатов с специальной низко профильной фольгой и\или активизация при подготовке проводящей поверхности в первую очередь процесса формирования химического адгезионного слоя;
в)использование для изготовления высокочастотных печатных плат материалов с малыми Dk и Df;
г) использование процессов травления, позволяющих формировать проводники с высоким фактором травления (например кислое травление «тентингом» с регенерацией рабочих растворов);
д) применение обратного сверления.
Реализация всех вышеперечисленных процессов позволит эффективно решать задачу разработки и изготовления высокочастотной радиоаппаратуры.
Литература
1. Albert Chen . “Why Signal Always Be Loss in a High Speed High Frequency Transmission Line”. Elite Material Co., Ltd. Taiwan, ROC.
2. John Coonrod, «Insertion Loss Comparisons of Common High Frequency PCB Constructions». Rogers Corporation.
3. George Milad, Jon Bengston and Albin Gruenwald, «Eliminating Ni Corrosion in ENIG/ENEPIG Using Reduction-Assisted Immersion Gold in Place of Standard Immersion Gold». Uyemura International Corporation, Southington, CT, USA.
4. Илья Лейтес, «Оборудование для многономенклатурного мелкосерийного изготовления сложных и прецизионных МПП» ТЭП №8 2016 г.
5. Илья Лейтес, Андрей Мусин, Сергей Кочетков, « Особенности производства печатных плат 6–7 го классов точности. Как изготавливать. На что обращать особое внимание.» ТЭП № 6 2015 г.